Table of contents
The realm of construction has embarked on a new revolution with the advent of 3D printed buildings. This emerging technology, while still in its nascent stages, promises to redefine the landscape of residential and commercial infrastructure. The prospect of creating bespoke designs from digital blueprints within days is not only exciting but also transformative for architects and engineers around the globe. Moreover, it ushers in a new era marked by efficiency, sustainability and affordability. So, how exactly does this remarkable innovation work? What are its implications for conventional construction methodologies? Let's embark on an intriguing journey into the world of 3D printed buildings.
The Mechanics Behind 3D Printed Buildings
In the realm of architectural design and construction, the advent of 3D printed buildings has brought about a revolutionary change. One might wonder how these digital models end up as tangible structures. It's all down to a process known as the layer-deposition technique.
Primarily, each construction begins with a computer-aided design (CAD), which serves as the digital blueprint for the building. This CAD model is then sliced into thousands of horizontal layers by the 3D printer's software. These layers are the basis for the physical construction of the building.
The actual building process is performed through an additive manufacturing method. The 3D printer, guided by the digital model, deposits construction material in layers, a method known as extrusion. This layer-by-layer deposition technique ensures precision and allows for complex designs to be brought to life. As per a Construction Engineer or Technology Expert's insights, this technique is capable of producing durable and resilient structures with greater design flexibility.
Imagine having the capacity to construct a building on-demand, with design limitations being a thing of the past. That's the reality of 3D printed buildings. The technology behind it is not just groundbreaking; it holds the potential to redefine how we approach construction and architectural design.
Potential Benefits Offered By This Innovation
The advent of 3D printed buildings introduces several benefits that have the potential to revolutionize the construction industry. One of the primary advantages is the rapid production time. 3D printing technologies enable structures to be fabricated much faster than traditional construction methods, significantly reducing project timelines.
Furthermore, the use of these technologies results in economic efficiency. As explained by environmental economists and sustainability experts, the costs of raw materials can be significantly reduced when using 3D printing techniques. This cost-effective solution can lead to substantial savings in the construction process.
Another considerable advantage is the reduction of waste. Traditional construction processes typically generate a significant amount of waste, contributing to environmental degradation. However, 3D printing technologies allow for precise, efficient use of materials, leading to substantial reductions in waste. This attribute aligns with the principles of eco-efficiency and sustainable construction, becoming a key factor in the transition towards more sustainable building practices.
In summary, the advent of 3D printed buildings brings about significant benefits, including rapid production, economic efficiency, and waste reduction. These advantages position 3D printing technologies as a revolutionary tool in the construction industry, paving the way for more sustainable, cost-effective building practices.
The Role Of Software In Facilitating Precision And Complexity
When it comes to revolutionizing construction, the advent of 3D printed buildings opens up new possibilities for intricate designs and architectural detailing. The key facilitator in this paradigm shift is advanced software applications. Software applications like CAD softwares are instrumental in enabling precision manufacturing and exploring advanced design possibilities. They provide architects with the tools needed to visualize and construct highly complex structures that were previously unattainable with traditional building methods.
One of the most groundbreaking techniques being employed is parametric design. This approach allows for the manipulation of design parameters to create complex, non-linear designs. An architect specializing in tech-based solutions observes that this allows for a level of precision and flexibility previously unseen in the construction industry. With the help of software, intricate architectural detailing is no longer a back-breaking task, but an easily achievable reality.
Moreover, the sophisticated ability of these software applications to simplify and enhance the construction process not only provides a more efficient way of building but also unlocks the potential for new architectural styles. In this regard, the role of software in 3D printed buildings is not just transformational, it's revolutionary.
Roadblocks And Challenges Paved By Advent Of This Technology
The upsurge of 3D printed buildings has undeniably brought forth a new era in the construction industry. Regulatory hurdles, however, pose as a significant roadblock to this pioneering technology. Ensuring compliance with building codes, a set of standards designed to ensure the safety and health of building occupants, is a challenge in the face of this innovative method. According to a policy analyst specializing in urban development, the adaptability of these codes to accommodate the unique specifications of 3D printed structures is yet to be fully explored.
In line with this, quality control standards also present a formidable hurdle. As an evolving field, the technology behind 3D printed buildings is still in the process of perfecting its outputs to meet stringent construction standards. It is paramount to ensure the durability, structural integrity, and safety of these buildings, hence the importance of robust and dynamic quality control measures.
Furthermore, the technology's widespread adoption faces hindrances due to the need for addressing concerns related to its environmental impact, cost-effectiveness, and scalability. While the potential of 3D printed buildings to revolutionize the construction industry is immense, it is evident that there are still numerous issues that need to be addressed before it can be adopted on a larger scale.
Similar articles

Revolutionizing Construction: The Advent of 3D Printed Buildings

Virtual Reality: A New Frontier in Gaming Experience
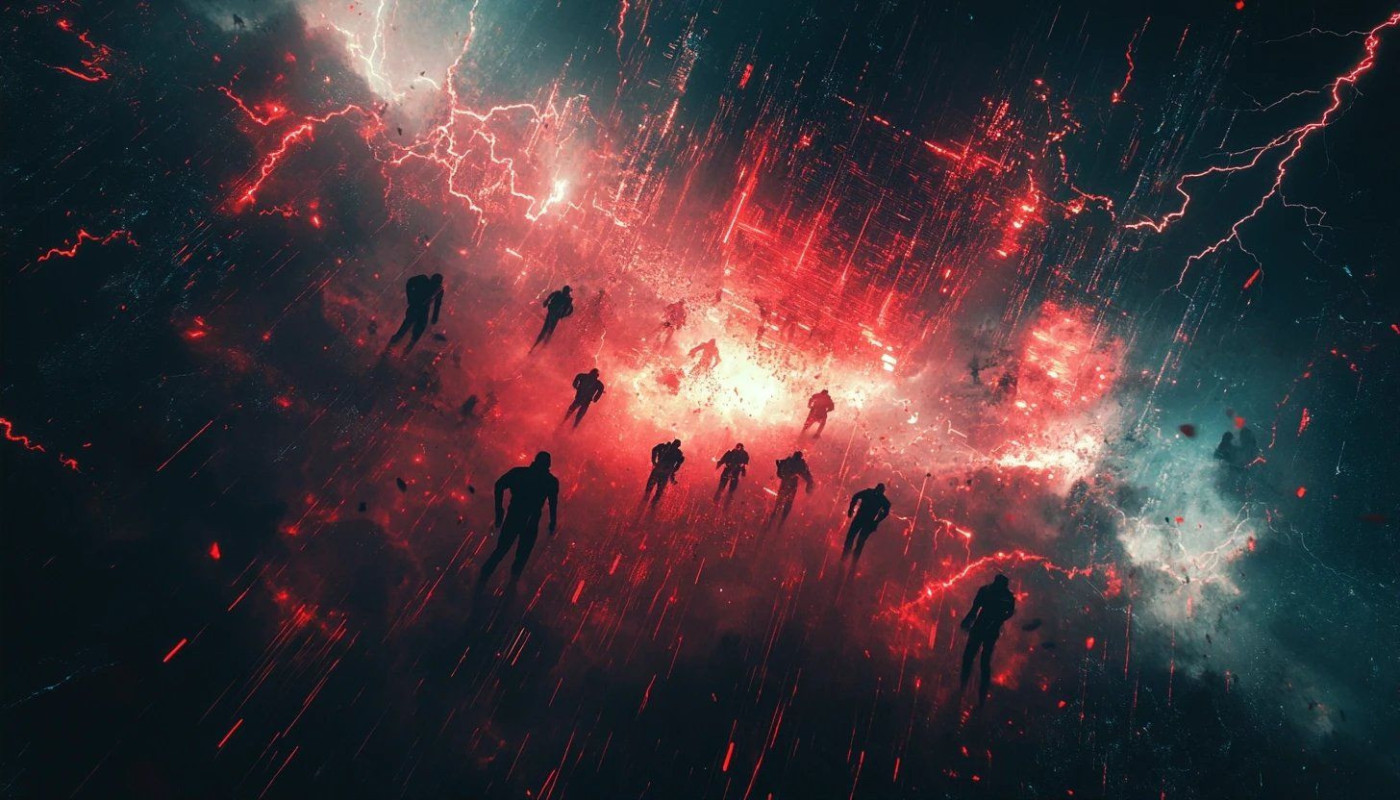